America’s Real Manufacturing Advantage
A new wave of software innovation is about to transform industry — and give the United States the chance for a lasting edge.
The industrial sector in the United States is rebounding. Manufacturers are boosting output, building new plants, increasing exports, and creating better-paying jobs that require precise skills—and in the process are helping lead the U.S. out of the long, stubborn slump that followed the market disruptions of 2007. A growing number of political and business leaders, economists, and commentators are taking notice, and talking about a domestic “manufacturing renaissance.” Some are saying it could add millions of new and well-paid jobs, unwind the U.S.’s long-standing trade deficit, and usher in a new era of growth and prosperity. This is a welcome point of view—much more beneficial than the idea, formerly in vogue, that the country could survive on services and finance, without much of a manufacturing industry. But it is, nonetheless, an incomplete point of view. Many of these manufacturing optimists are basing their forecasts mainly on transitory changes in energy supply and relative labor costs that are not likely to provide the kind of long-term improvements they envision.
We are hopeful about the future of manufacturing in the U.S. for a more fundamental reason. It is the economy best positioned to seize on deeper changes that can lead to a real, sustainable manufacturing renaissance, one based on software technology and its profound effect on the entire manufacturing value chain.
The pace of change in global manufacturing is faster right now than at any time in recent history. The technology and practice of large-scale manufacturing are moving into a new era of proficiency—not just typified by improvements in established processes, but taking the form of a software-powered series of new production systems that are qualitatively different from those of previous years. All aspects of manufacturing will be affected, including the way companies address customer needs and wants, research and development, the product development and production process, and the platforms and footprints employed in execution, testing, and servicing (see sidebar).
Software’s Impact on the Five Steps of Product Development and Production
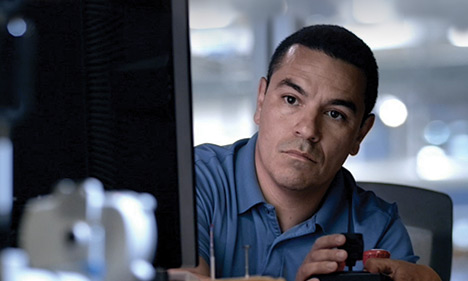
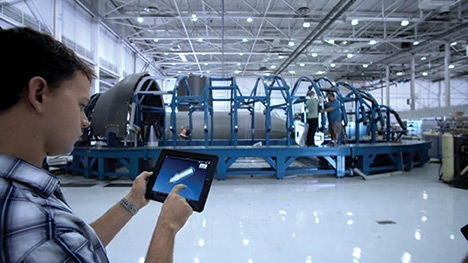
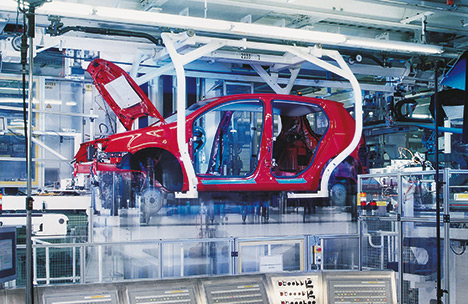
The changes under way will increase productivity, efficiency and innovation, speed-to-market, and flexibility, which will in turn lead to a powerful new cycle of growth and value creation: an era of virtual-to-real manufacturing. As a result, the trade-off between efficiency and customization—which has constrained manufacturing since the Industrial Revolution began—will no longer be nearly as important, and manufacturers will gain new abilities to create and maintain products that more specifically fit what people want and need.
The advanced manufacturing facilities of today and tomorrow are clean and replete with robots, computers, lasers, and other ultramodern machine technologies. The most common tool a production worker carries at the newest auto plants in the Carolinas, Michigan, and Tennessee is not a wrench or screwdriver. It’s an iPad. The next chapter is about to be written in the history of industry. Among manufacturers, competitive advantage will flow to those that can adapt most quickly in this changing environment.
With a proven track record in innovation, software development, and university education, the United States is poised to reassert the manufacturing leadership it has been ceding to competing countries in recent decades. And the economic stakes for doing so are high. If the opportunity is seized aggressively, it will provide increasing numbers of skilled, well-paid jobs that can support the middle class in the 21st century. Beyond job creation, manufacturing plays a vital role in promoting innovation and long-term competitiveness. Every dollar generated by manufacturing supports US$1.48 of additional economic activity, according to the Manufacturing Institute, compared with $0.54 for retailing. And although manufacturing accounts for 12 percent of U.S. GDP, it provides nearly 70 percent of private-sector R&D and 90 percent of patents issued. If the U.S. can recharge its manufacturing prowess, it will accelerate its own economic growth—and that, in itself, could be an engine promoting growth around the world.
But whether the U.S. can seize the opportunity is not certain. Competitive advantage in the 21st century will be influenced by factors such as cheap energy and wage rates—but it will be decided by the ability of countries and regions to enable advanced design and manufacturing. Action is needed now to reinforce the innovation culture in the U.S., to nurture the kinds of institutions that can support a vibrant manufacturing industry, and to build new types of educational support, including the apprenticeships and other experience-based programs that will help the U.S. workforce.
Competitive advantage in the 21st century will be influenced by factors such as cheap energy and wage rates—but it will be decided by the ability of countries and regions to enable advanced design and manufacturing.
Deconstructing the Renaissance
Although some aspects of the new manufacturing renaissance have been gaining force for several years, their impact is just now being noticed. They include renewed investment in U.S. manufacturing plants and equipment, and some re-shoring of production jobs from Asia and other places. Much of this activity, however, reflects renewed competitive advantage that may not continue to increase at its recent rate as the underlying trends change.
The most visible of these trends has been the availability of inexpensive shale-based oil and natural gas in the United States. By lowering energy prices and broadening access to the supply of gas, this has created a competitive advantage for the country as a manufacturing location. By late 2013, natural gas was selling in the U.S. at roughly a third the price it commanded in Europe, and at a quarter of the price in Asia. This makes the U.S. particularly attractive for manufacturers in energy-intensive industries such as chemicals and fertilizer, steel and aluminum, and plastics. For well over a decade, there had been little U.S. investment in these businesses; some seemed in danger of departing altogether. Now, as a result of new energy supplies, some $100 billion of investment is flowing into energy-intensive manufacturing industries in the U.S., with more than 100 new plants planned or under construction.
For example, the Austrian steel-based technology and capital goods maker Voestalpine Group is building a new iron-ore plant on Corpus Christi Bay in Texas. Once it opens (scheduled for 2016), it will produce up to 2 million tons per year of hot briquetted iron (a feedstock for steel mills). The plant will use a natural-gas direct reduction process that is more environmentally friendly than the traditional coke-based technology and will help Voestalpine meet ambitious internal energy efficiency and climate-protection objectives. V&M’s tubular steel plant in Youngstown, Ohio, is another example. The plant uses low-cost gas, and supplies tubular steel to the expanding U.S. oil and gas industry for drilling.
Recent shifts in labor costs have also changed the competitive landscape. A 2013 analysis by the consultancy AlixPartners estimates that the cost of offshoring manufacturing to China will equal the cost of manufacturing in the U.S. by 2015. The large labor-cost advantage that Asian competitors enjoyed in the 1990s and early 2000s has narrowed over the last 10 years. When the higher productivity of North American workers (three times as high as that of workers at some low-wage competitors) and the often minor share of labor cost in the total cost calculation are factored in, the labor-cost advantage is insignificant.
These two forces—low-cost energy and labor equivalence—have significantly improved U.S. competitiveness. A study by the Information Technology & Innovation Foundation estimates that some 500,000 manufacturing jobs have been created in the country since 2010, supported in part by re-shoring in industries as varied as aerospace, appliances, autos, textiles, and toys. But changes in energy and labor prices are not likely to provide lasting advantage. Other countries will tap into their gas resources with similar technologies, and global trade in liquefied natural gas will inevitably increase, narrowing the price differential. The change in labor costs will most likely be moderated by increasing productivity in other regions, which will limit future improvements in competitive advantage for the United States.
Fortunately for the U.S., one other key trend driving the domestic resurgence of manufacturing is less likely to be shared. The MIT Forum for Supply Chain Innovation and Supply Chain Digest surveyed 340 supply chain managers in 2012, and found that in addition to costs, an important decision driver for those considering re-shoring is faster speed-to-market. Indeed, as corporate leaders make decisions about plant location, a key risk they face is uncertainty about future growth in demand. One way to reduce that risk is to locate manufacturing facilities close to markets, enhancing their ability to understand customer requirements and react quickly throughout the entire value chain when requirements change. Thus the U.S. will be favored for production that is slated for U.S. consumption.
To make the most of the manufacturing renaissance, however, the U.S. will also have to compete as a manufacturing location for high-value-added products designed for export. It is for this reason that the advantages the U.S. offers—as a base for the advanced, virtual-to-real manufacturing that is transforming the global industrial landscape—will become increasingly important. To understand why this transformation is so profound, it helps to look at how today’s advances fit within the historical context of manufacturing technology.
Efficiency, Innovation, and Flexibility
From its beginnings in the 18th century, the Industrial Revolution was all about efficiency and affordability. Previously, all goods had been made from scratch by craftsmen, who tailored each item—and often the process of making it—to the requirements and circumstances of each customer. But making things this way was expensive and slow. Few people other than the wealthy could afford to own much more than the simplest household objects and rudimentary tools.
Then, as industrialization advanced from the late 18th through the 19th century, the efficiencies enabled by steam power and mass production drove prices of manufactured goods to levels low enough to be affordable for the mass market. Manufacturing efficiency made a further leap forward in the 20th century with the advent of the moving assembly line, more systematic approaches to operations, and advances in technology.
But some things were lost in the move to mass production, including the ability to shift production quickly to new goods, to incorporate new features, and to offer variety in product lines.
The next major cycle of manufacturing advancement, which is in its early stages now, greatly reduces the need to make this trade-off, thanks to the connection of increasingly powerful software with dramatic leaps in the performance of hardware.
The use of computer software in manufacturing is nothing new. The first numerically controlled machines date to the 1940s, when engineers adapted machine tools to accept commands via punched tape. These evolved over the next few decades to become sophisticated computer numerical control (CNC) machines, which perform a vast range of tasks such as milling, laser cutting, and welding. Computers were also adapted to product design, first in the 1960s, and then more extensively in the 1970s as computer-aided design hardware and software proliferated.
Since the early 2000s, however, automation and design software have begun to merge, and manufacturing software in general has become far more sophisticated. The result is an integration of the virtual and physical worlds. Before anything is constructed or set into physical operations, it can be simulated, modeled, and tested—inexpensively and rapidly. Virtual design, planning and development of products and the production process, and optimized control are having a powerful effect, especially in highly complex manufacturing systems such as auto assembly. This has led to three important benefits: further gains in efficiency, a step-change improvement in production innovation and speed-to-market, and a new ability to incorporate flexibility into mass production.
• More efficient production. To this day, manufacturers continue to lower costs and raise efficiency by improving processes and upgrading technologies and machinery. There are still significant productivity gains to be made in many sectors of manufacturing, especially in emerging economies. Coca-Cola Vietnam, for example, increased its production rate by 30 percent recently, when it replaced some of its legacy machinery with automated hardware and software. This enabled the company to meet demand that has grown by 35 percent per year since 2009.
More efficient machinery and controls also pay dividends in energy savings—boosting productivity while reducing manufacturers’ carbon footprints. An auto plant with a daily output of 1,000 vehicles can consume several hundred thousand megawatt-hours of electricity per year—as much as a medium-sized city. The electric motors used to drive conveyer systems, robots, and other machinery use two-thirds of this power, and optimized control systems can reduce their consumption by as much as 70 percent. Further efficiencies are within reach. Siemens, for example, has joined with Volkswagen and the Fraunhofer Institute for Machine Tools and Forming Technology to study ways to make robots more energy efficient. Simply optimizing the software that controls their movement patterns can save up to 24 percent in energy costs.
• Innovation and speed-to-market. The ability to model, visualize, and test in the world of virtual-to-real manufacturing is changing the nature of innovation. Research and development and operations can now become a single integrated process extending from design through product development and manufacturing to aftermarket service.
The ability to model, visualize, and test in the world of virtual-to-real manufacturing is changing the nature of innovation.
The Mars Curiosity rover, created by the National Aeronautics and Space Administration (NASA), which landed on Mars in August 2012, is a vivid example of how sophisticated software technology has become. The rover is the size of a small SUV and contains, among other things, a small nuclear power plant and two chemistry laboratories. Previous unmanned space missions, with smaller and less delicate payloads, were dropped onto the planet surface by parachute, with a rough landing cushioned by airbags. The Curiosity needed to be set down much more gently, as well as more accurately. Engineers designed an entry vehicle that would be slowed by parachute at first, then fly itself the rest of the way using thruster rockets, slow to a hover 60 feet above the planet, and finally lower the rover carefully to the surface.
The big question was, Would it work? Traditional practice runs were not an option, since conditions on Mars could not be replicated—or even approximated—on Earth. Doug McCuistion, the former NASA director who led the Mars Exploration Program, notes some of the complexities: “Thousands of different software-driven events had to occur throughout the seven-minute landing process. Seventy-six pyrotechnics had to fire, all at exactly the right time. If any one of those events is not successful, you have a mission failure.” McCuistion says he was confident about the landing because of the extensive trial runs NASA had been able to simulate in the virtual world, combined with targeted testing. The technology used, he explains, “is a combination of deep analysis through software coupled with modeling, which allowed us to develop simulations of amazingly complex descent systems, and to run thousands and thousands of iterations. It could only be done with the design and simulation software we have today.”
The visualization and simulation software used in the Mars Exploration Program, provided by Siemens, is similar to the software that manufacturers such as Ford, Unilever, Canon, Dyson, and Callaway use to design and optimize production processes before changes or alterations are made to products or production machinery. This enables the companies to bring products to market much more quickly and efficiently than in the past. The further impact of visualization software will be greatest in discrete manufacturing (production of distinct items such as autos, appliances, or toys), whereas process manufacturing (products such as oil and gas) will benefit mostly in the design of the production facilities.
When simulation software is used on the factory floor alongside the machinery that it models, it gives operators a “digital twin” of the machine on screen, which looks and acts exactly like the machine itself. Index-Werke, in Esslingen, Germany, has built this virtual machine capability into its state-of-the-art CNC lathes. Operators can test and optimize a new process without taking the machine out of production. According to Eberhard Beck, the head of control technology at Index-Werke, the digital twin approach increases operational productivity by 10 percent, and reduces machine downtime during the setup process for new jobs by 80 percent.
• Greater flexibility. The integration of virtual and real production is making mass customization—the ability to make more customized and varied products without adding significant cost—a reality. When Ford’s Model T assembly line started up 100 years ago, the company famously offered the car in “any color you want, so long as it’s black.” Today, Ford can build its F150 pickup truck to customer specifications in millions of possible configurations involving the body, drivetrain, wheels, accessories, and trim.
Ford has been a leader in designing flexible production that not only enables mass customization, but also allows the company to build different vehicle models in the same plant, or build the same model in dissimilar plants around the world all using, and maximizing, the same global manufacturing standards. This capability is increasingly important as automakers produce vehicles in different configurations—including gasoline, electric, and hybrid powertrains—for different markets. To make this possible, Ford partnered with Siemens to create an “enterprise bill-of-process” software capability that allows engineers to simulate the entire assembly process at different plants. The application was recognized in the industry through Ford’s “Manufacturer of the Year” award from the Manufacturing Leadership Council in 2013.
“Our goal is to lead the industry in flexible manufacturing and global vehicle program development,” says Alan Baumgartner, technical leader of virtual manufacturing at Ford. “It starts with having a software system that enables us to build vehicles that are innovative and loaded with technology, but in a way that makes them affordable. We can do that by driving standardization and reuse of our vehicle programs on a global scale.”
Another game-changing manufacturing innovation enabled by software and advanced technology is the increasing use of three-dimensional (3D) printing and additive manufacturing technology in a factory setting, wherein products are built by machines laying down one thin layer of material at a time according to digital blueprints. The technology has been in use since the 1980s, but until recently applications in industry had been limited to prototyping parts or products for analysis and testing. Increasingly, 3D printing technology can fabricate complex, high-value parts using powdered metals and lasers. General Electric, for example, is printing cobalt–chromium fuel nozzles for jet engines, as well as other engine components.
Advances in 3D printing technology are enabling customization at increasingly granular levels. Medical device manufacturers can now make personalized orthopedic joint replacement kits custom-fitted to an individual’s anatomy. The 3D printers might be located in hospitals rather than in a central production facility. Another application, which could have significant impacts for product life spans and inventory management, would be the manufacture of replacement parts where demand is both low and uncertain.
Over the next couple of decades, we will see continued improvements in each of these three areas: Ongoing gains in efficiency will raise productivity and add value for all manufacturers. Innovation will flourish and speed-to-market will increase as virtual-to-real manufacturing becomes more commonplace. And mass customization will usher in a new era of choice and flexibility for manufacturers and consumers—in some ways renewing many of the advantages of the craftsman era that were either lost or deemphasized during the era of mass production, but in a modern factory setting.
Advanced manufacturers are actively pursuing the next frontier in production capabilities, which we refer to as Industry 4.0. Still largely in the conceptual stage, the next cycle of software integration, advanced digitization, and networking will harness “big data” feedback in real time from customers and suppliers, as well as information about the operation of the production machinery and the product as it is used. Today, for example, Apple’s iPhone can send diagnostic data back to the company about the way the operating system and hardware are performing. Production machines will be self-optimizing—able to look at what they are doing, change themselves to operate more effectively, and thus continually improve their own productivity, efficiency, speed, and flexibility. Managers and production workers will still be in charge, naturally, but they will be controlling software and processes, rather than the machinery itself.
All these advances depend on sophisticated software design and architecture, which explains why the U.S. is well positioned to succeed as the manufacturing transformation proceeds. The U.S. remains the most advanced country for software development: Sixty-five of the PwC Global Top 100 Software Leaders are headquartered in the U.S., and an analysis by the Business Software Alliance found that 79 percent of the $243 billion software revenue from the top 100 firms in 2011 was accounted for by U.S. companies. Clusters of software expertise exist in other countries, of course. Germany, for example, leads in shop-floor control software, because of the strong relationships between leading machine companies and control providers. India is known for its software-based services. But the U.S. leads in the particular kind of decision-support software architecture and programming that will be most essential in visualization, modeling, and other ways of integrating the virtual and real worlds of manufacturing. This lead arose partly from the country’s traditionally strong position in computer-science education and research, but also because of the culture of innovation, opportunity, and entrepreneurialism that grew up around the industry in Silicon Valley and has drawn the best talent from around the world. To preserve this advantage, however, the U.S. needs to take action.
A Sustainable Renaissance
What can U.S. business leaders and policymakers do to ensure that the manufacturing renaissance solidifies, gains force across industries, and realizes its potential in fostering economic growth during the years ahead?
Action should be focused in three areas: maintaining the U.S.’s established culture of innovation, nurturing the institutions that have made the U.S. a leader in software, and raising the quality of education and training, particularly in those aspects that will matter to manufacturing. Above all, policy needs to reduce uncertainty, reflecting broad agreement and a focus on long-term success.
• Innovation culture. One of the most important things that business leaders will look for as they locate advanced manufacturing facilities is access to the leading-edge research and technology development that flows from major universities, along with the availability of engineers, executives, and production workers with the right skills. To ensure the continued robustness of U.S. R&D, in fact, it is necessary to make sure that manufacturing itself stays in the United States. As Dow Chemical chairman and CEO Andrew Liveris notes in Make It in America: The Case for Re-Inventing the Economy (Wiley, 2011), “You cannot separate innovation from manufacturing. Where manufacturing goes, innovation inevitably follows.”
One simple initiative to support U.S. innovation is to reform the research and development tax credit (referred to in current law as the “research and experimentation” tax credit). It should be extended, simplified, and made permanent. There is broad bipartisan support for this change. The U.S. was a leader in encouraging innovation when the tax credit was enacted in 1981, but other nations were quick to emulate—and in many cases to surpass—the U.S. approach. Worse, this tax credit has always been treated as temporary; Congress extends it every few years, sometimes on an ad hoc basis.
One simple initiative to support U.S. innovation is to reform the research and development tax credit.
• Nurturing institutions. Another imperative should be to preserve—and to further build and strengthen—the institutions that enabled the U.S. technology and software sectors to grow and flourish in the first place. These include the national research laboratories and the university system, but also the venture capital industry, which is a crucial—and unique—bridge between academia and the marketplace. State, local, and public–private initiatives should also aim to foster the continued growth and development of the regional clusters of technology and software innovation that have played a crucial role in building the United States’ advanced manufacturing capacity and productivity. These are a vital part of what Harvard Business School professors Gary Pisano and Willy Shih refer to as the U.S. “manufacturing commons” (in Producing Prosperity: Why America Needs a Manufacturing Renaissance [Harvard Business Press, 2012]), which provides the expertise, skilled workers, and infrastructure that manufacturers need.
• Education and training. To enable real job growth in the coming era of advanced, virtual-to-real manufacturing, the U.S. will need to build on its strengths in education—such as its leading research universities—while filling gaps that have appeared in recent decades. There are significant shortfalls in STEM (science, technology, engineering, and math) education—particularly technology and engineering. U.S. students, the National Science Board reports, are earning only 11 percent of the world’s 4 million undergraduate S&E degrees, compared to 21 percent in China and 19 percent in the European Union. Gaps at the primary- and secondary-school levels are also wide. Although STEM knowledge and skills are improving, U.S. students still lag behind international averages in mathematics.
Most of all, the public and private sectors must close the nation’s training gap. The commonly used phrase “skills gap” implies that this is a matter of capable individuals needing proficiency, but the problem is broader and more systemic. The U.S. will never meet its future challenges until managers and policymakers put the burden on those who do the training, rather than those who need to be trained. In Why Good People Can’t Get Jobs: The Skills Gap and What Companies Can Do about It (Wharton Digital Press, 2012), Wharton professor Peter Cappelli notes that in 1979, U.S. workers received an average of 2.5 weeks of training per year. By 1995, the average company offered just under 11 hours per year. In 2011, Accenture found, only 21 percent of U.S. employees had received any employer-provided training in the previous five years.
To succeed in advanced manufacturing workplaces, workers need to possess the production skills to set up, monitor, and control the manufacturing processes, and the process design and development skills to continuously improve them. They will need strong computer skills, the ability to understand sophisticated production processes, and the knowledge of how to work effectively in teams.
A number of pilot programs are under way today that show how the training gap can be closed. Siemens is a partner in an apprenticeship program in North Carolina, along with Apprenticeship 2000, Central Piedmont Community College, and six other technology corporations. High school graduates joining the program alternate between studying at the college and working at Siemens’s advanced turbine plant in Charlotte. Students are paid while training and attending school for three and a half years, and upon graduation are offered full-time jobs at competitive salaries—higher, in fact, than the average salaries for graduates with four-year liberal arts degrees. Best of all, they have an associate’s degree in mechatronics (a multidisciplinary field that includes mechanical, electrical, control, and computer engineering), a journeyman’s certificate recognized by thousands of companies, and a job, with no loans to pay off. IBM’s P-Tech initiative, launched in 2011, is another example. (P-Tech stands for “Pathways in Technology Early College High School.”) The program starts in ninth grade, offering an integrated high school and college curriculum focused on STEM subjects, along with workplace skills such as leadership, communication, and problem solving. Students receive both their high school diploma and an associate’s degree in computer information systems or electromechanical engineering technology, and are first in line for entry-level positions at IBM.
Programs like these are models for the kind of experience-based educational paths that must be expanded nationwide. These programs are similar to Germany’s youth apprenticeships, which have helped enable that nation to maintain a leading position in manufacturing and to boast the lowest youth unemployment rate in the European Union. At 7.5 percent, the jobless level among young people in Germany is less than a third of the E.U. average rate of 24 percent, and less than half the U.S. rate of 16.2 percent. An extensive, well-supported apprenticeship system, and other programs through which people receive hands-on experience coupled with academic training, will prepare young Americans for the jobs that advanced manufacturing will offer: skilled, well-paid, and secure jobs that can support a new middle class. Developing such programs will require a partnership among government, educational institutions, industry, and labor—and will provide a collective power no single sector can match.
The Case for Optimism
Public perception about manufacturing has been changing for the better in the U.S. over the past few years. From the 1980s through the 1990s, many policymakers and prominent economists had argued that the decline of manufacturing in the U.S. was an inevitable evolution, and that the expanding service and financial sectors would continue to provide growth and prosperity. The dot-com bust in the early 2000s, the housing and financial debacle later in the decade, and the worsening employment situation for workers in the U.S. have revealed the weaknesses of that argument.
Today, policymakers and consumers are becoming more receptive to the idea that manufacturing is an important source of jobs, competitiveness, and economic strength and security, even if some are basing their expectations of a manufacturing renaissance on the wrong factors. The federal government has been hands-on in convening business leaders and researchers to create new programs to foster manufacturing, focusing school curricula on STEM subjects, providing funding for community college grants to expand job training, and proposing new programs such as the Advanced Manufacturing Partnership and institutions such as the Digital Manufacturing and Design Innovation Institute.
One important effect of the current debate has been to further build public support for manufacturing. A growing body of intellectual capital—including research conducted by organizations like the Brookings Institution, the Business Roundtable, the Manufacturers Alliance for Productivity and Innovation, and the National Association of Manufacturers, as well as articles and books by an array of thought leaders—is helping bring about a change in the American psyche.
Nevertheless, manufacturing still has a branding problem. Lacking knowledge of what the future of advanced manufacturing looks like, too many students, parents, educators, and policymakers reflexively associate manufacturing with archaic factory settings and low pay. This suggests a need for further education about the opportunities for high-paying, high-tech jobs in the manufacturing facilities of today and tomorrow.
The coming era of advanced, virtual-to-real manufacturing will reorder the global business landscape for decades. The key success factors for companies, nations, and regions will be innovation, software, and education. Manufacturers should be examining their operations, looking for opportunities where software and advanced technology can lead to step-change improvements. Manufacturers that capitalize on these changes across their entire development and production process will set the tone that others will be forced to follow to remain competitive. The U.S., given its historical strength in innovation, its strong position as the world leader in software development, and its robust education infrastructure, is well positioned to lead in this cycle. To seize the opportunity, the business and policy communities will need to work together to build on these strengths. If they do, the conditions will be in place for a new approach to manufacturing, ensuring that the investment and expansion we have seen over the last several years can continue and grow, and eventually lead to an age of enlightenment in which advanced manufacturing becomes a central pillar in building a U.S. economy—and a stronger middle class—for the 21st century.
Reprint No. 00240
Author profiles:
- Helmuth Ludwig is chief executive officer of Siemens Industry USA. He is also an adjunct professor at the Cox School of Business at Southern Methodist University and a member of the board of the Manufacturers Alliance for Productivity and Innovation.
- Eric Spiegel is president and chief executive officer of Siemens Corporation. He was formerly a senior partner at Booz & Company, and is the coauthor (with Neil McArthur) of Energy Shift: Game-Changing Options for Fueling the Future (McGraw-Hill, 2009). He is vice chair of the Education and Workforce Committee at the Business Roundtable and a member of the board of the U.S. Chamber of Commerce.
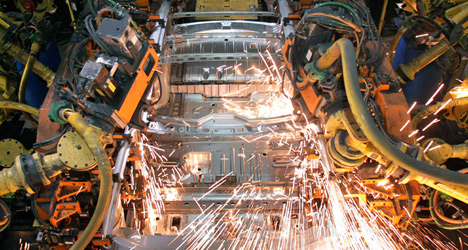